Dive Deep: Insights About Aluminum Casting Processes
Dive Deep: Insights About Aluminum Casting Processes
Blog Article
Explore the World of Aluminum Spreading: Expert Techniques and secrets
In the realm of production, light weight aluminum spreading stands as a critical process, important for the creation of a vast selection of items. Behind the apparently uncomplicated method exist a wide range of elaborate facets, typically unbeknownst to lots of. As we navigate via the globe of light weight aluminum spreading, there exists a realm of expert secrets and strategies that can boost the quality of the end products and streamline the production process. By revealing these hidden treasures and exploring the nuances of this craft, an entire brand-new measurement of possibilities emerges, guaranteeing to transform the way we perceive and engage with light weight aluminum casting.
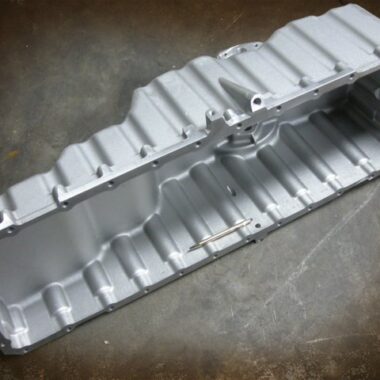
The Basics of Light Weight Aluminum Casting
Light weight aluminum spreading, an essential process in production, involves the putting of molten light weight aluminum into a mold to attain wanted shapes and frameworks. This functional strategy is extensively made use of across numerous markets because of light weight aluminum's exceptional residential properties such as high strength-to-weight ratio, rust resistance, and thermal conductivity.
The process starts with the melting of light weight aluminum in a furnace at temperatures exceeding 1220 ° F(660 ° C ) When the aluminum reaches its liquid state, it is put right into a pre-designed mold dental caries. The mold, normally made from products like steel or sand, determines the final form of the actors aluminum component.
After putting, the aluminum is delegated solidify and cool within the mold and mildew - about aluminum casting. This cooling duration is crucial as it determines the stability and top quality of the end product. When strengthened, the mold is removed, exposing the recently developed aluminum spreading
Expert Tips for Effective Casting
To accomplish optimal results in aluminum casting, thorough attention to information throughout the mold and mildew design phase is critical for guaranteeing successful end results. Surveillance and controlling the steel temperature level throughout the spreading procedure can help avoid issues such as premature solidification or porosity in the final product.
A well-prepared mold surface can add to much better steel flow, reduced turbulence, and boosted surface coating on the actors component. By paying close focus to these expert tips, suppliers can improve the top quality and performance of their light weight aluminum casting procedures.
Advanced Methods in Aluminum Casting
Making use of innovative approaches and ingenious methods, the world of light weight aluminum casting has seen a considerable evolution towards advanced techniques that press the borders of traditional techniques. One such method is vacuum spreading, which entails developing a vacuum setting to eliminate air from the mold and mildew cavity, leading to higher quality and even more complex spreadings with lowered porosity. Furthermore, investment spreading, likewise known as lost-wax spreading, is a refined method that allows for complicated shapes and thin walls, causing detailed and precise my sources light weight aluminum components.
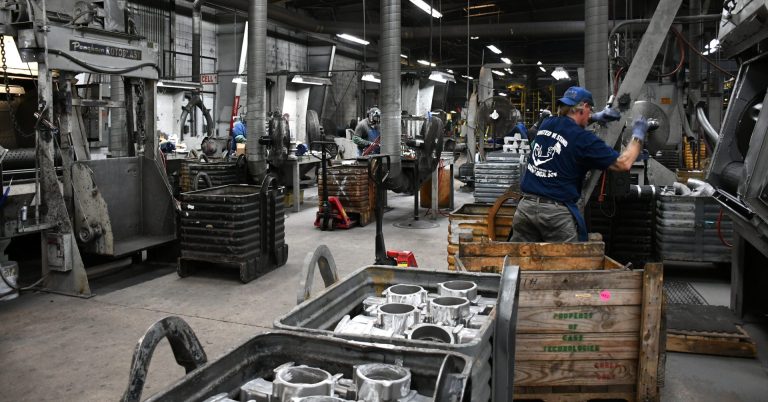
In addition, advanced simulation software application plays a critical role in enhancing casting designs and forecasting potential defects, permitting adjustments to be made before the actual spreading procedure begins. By accepting these advanced methods, suppliers can boost their light weight aluminum casting abilities to brand-new elevations, fulfilling the needs of modern markets with precision and development.
Comprehending Various Casting Approaches
In the realm of manufacturing, a detailed understanding of various casting techniques is necessary for attaining optimal lead to metal construction processes. Various casting techniques provide distinct advantages and are picked based on aspects such as the complexity of the style, production volume, material needs, and price factors to consider. One of the most usual casting techniques is sand casting, where a mold is produced making use of sand as the key material. Sand spreading is functional, affordable, and appropriate for producing huge webpage components.
Another prominent spreading technique is die casting, which includes injecting liquified steel into a mold and mildew cavity under high stress. Pass away casting is known for its high precision, smooth surface coating, and the capacity to produce complex shapes with limited resistances. Gravity spreading, on the various other hand, counts on gravity to fill up the mold and mildew cavity with molten steel. This technique appropriates for creating simpler forms and is cost-efficient for tiny to tool manufacturing runs. By recognizing the subtleties of different casting approaches, producers can make informed decisions to maximize their production procedures and accomplish the preferred outcomes.
Making Best Use Of Performance in Spreading Workflow
With a strong grip of the subtleties of various casting approaches, producers can enhance their procedures to enhance performance in steel fabrication processes. Making best use of efficiency in casting operations calls for a systematic strategy that focuses on optimizing every action of the casting process.
Moreover, purchasing sophisticated innovation and equipment can dramatically improve effectiveness in casting procedures. Automated systems, robotics, and computer-aided design (CAD) software program can improve procedures, decrease errors, and rise output. Additionally, training employees on the most recent methods and ideal practices can likewise add to making the most of performance in casting operations.
Routine maintenance of devices and devices is crucial to minimize and prevent breakdowns downtime - about aluminum casting. Executing a positive maintenance routine can aid identify prospective problems prior to they intensify, making sure smooth procedures and undisturbed manufacturing. In general, by focusing on performance and continual improvement, suppliers can optimize their spreading procedures and stay affordable in the sector
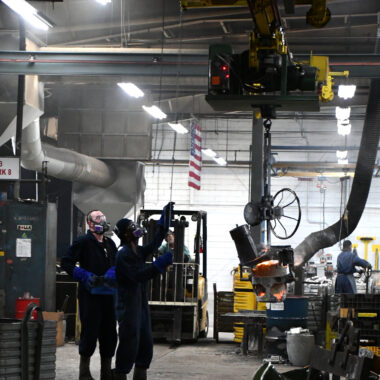
Verdict
Finally, the world of aluminum casting uses a wide variety of possibilities for those looking to develop elaborate and resilient steel objects. By mastering the essentials, using insider suggestions, and checking out sophisticated her comment is here techniques, people can attain terrific success in their spreading endeavors. Recognizing the various spreading approaches and enhancing effectiveness in procedures are vital components to attaining top notch lead to light weight aluminum casting. With commitment and method, one can truly unlock the potential of this versatile metalworking process.
One such method is vacuum casting, which involves developing a vacuum setting to remove air from the mold and mildew cavity, leading to greater high quality and even more intricate castings with reduced porosity (about aluminum casting). Additionally, investment casting, likewise recognized as lost-wax casting, is a refined approach that permits for intricate shapes and slim walls, resulting in detailed and accurate aluminum components
One of the most usual spreading techniques is sand casting, where a mold and mildew is produced using sand as the main material.Another popular casting technique is pass away casting, which involves injecting liquified metal right into a mold and mildew tooth cavity under high pressure. Understanding the various casting approaches and optimizing efficiency in operations are key elements to achieving top notch results in light weight aluminum spreading.
Report this page